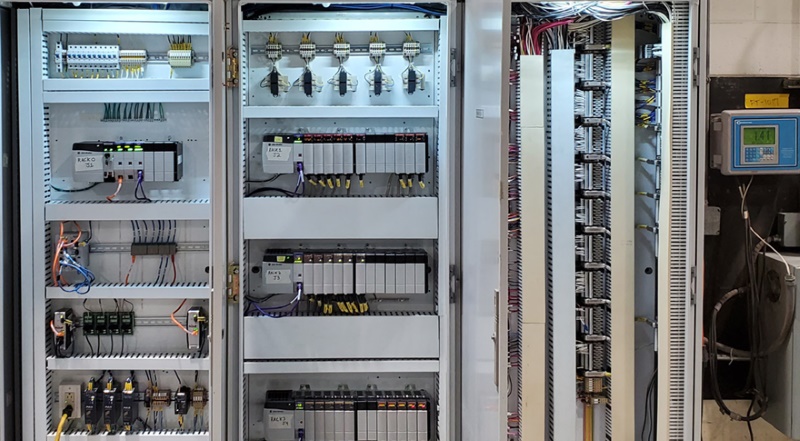
An Ivy League university on the East Coast* contracted Thermo Systems in Fall 2019 to improve optimization, reliability and scalability for their campus chilled water facilities — a 13,000-ton facility serving campus buildings including research labs.
PROJECT GOALS
- Upgrade to current PLC technology
- Update/standardize HMI graphics
- Replace HMI servers and workstations
- Document the system
- Survey the network
- Increase resiliency & decrease costs
PROJECT CHALLENGES
- Short installation timeline in order to minimize impact to plant/campus
- Difficult logistics (basement) and limited space
- Unavailable backplane replacement
- Remote differential pressure readings via Modbus through a network managed by others
- Unknown Modbus communication throughout facility
- Uncommented existing PLC program
- Unlabeled cabling
- Conflicting panel drawings
SOLUTION BENEFITS
- Complete updated panel drawings for ease of troubleshooting
- Documented sequence explanation
- Industry-wide communication protocols
- Ability to further expand and optimize
- Same PLC hardware as other plants on campus
- Maintainability with common programming interface Studio 5000®
- Programming standardization
- Additional vendor support
- Spare part availability (next-day, off the shelf)
- Documented PLC program
- Standardized graphics
- Dedicated space for critical infrastructure
Thermo Systems applied its extensive knowledge and expertise to successfully deliver this project on time and on budget. Our team utilized a detailed implementation plan that reduced risk, included a fallback plan, and project timeline to meet the client’s tight deadline. Leveraging a team of experienced automation and plant engineers, Thermo Systems provided a turnkey installation of current technology. This Ivy League university now has a modern PLC Control System for their chilled water facilities and can feel confident that they have the technology needed for optimization and future cost savings.
*Name of university withheld at request of the client.